炭黑產業網據橡膠快遞消息,隨著工業4.0繼續在全球多個行業的引入,輪胎制造商和供應商正在探索通過實施一系列互聯技術來提高生產能力和可持續性的方法。通過利用人工智能、機器學習和分析軟件等智能技術,輪胎制造商正在全面改革他們的制造技術、產品處理流程和分銷業務。
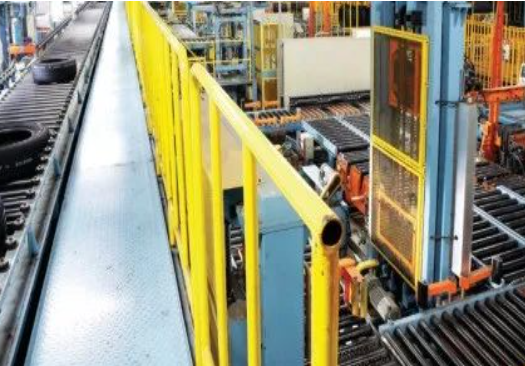
VMI 集團研發副總裁 Gerlof Korte 表示:“輪胎制造商更加關注全整個流程鏈的自動化。比如說輪胎廠,擁有密煉、半成品、成型、硫化以及檢測中心等。我們發現,制造商正試圖減少半成品的制備時間,將更多的半成品制備過程合并到輪胎成型過程中。”據 Korte 估計,勞動力約占輪胎制造總成本的50%。他表示,如果輪胎制造商經營一家每天可生產2萬條輪胎的工廠,大約需要750名員工。“每條輪胎的人工成本約為25歐元,按這個數字來算,成本是較高的。所以,人們在不斷尋求更高程度的自動化,而我們所做的機械就是盡可能地限制勞動力的數量。”位于斯里蘭卡 Badalgama 的GRI(Global Rubber Industries)新工廠生產各種輪胎,需要公司在生產現場安裝一系列多功能的自動化設備。GRI 執行董事 Ananda Caldera 表示:“我們在這里擁有非常龐大的產品組合,因此我們使用的所有自動化機器必須適合我們生產的所有類型的輪胎,這與普通的汽車輪胎工廠不同,所以我們在為自動化流程選擇機械時非常謹慎。我們有一臺來自意大利柯美尼奧(Comerio)的壓延機,可通過計算機系統實現完全自動化,這是確保產品質量和可持續性的必要條件。”這些現代機械得益于先進的機器人、軟件和高精度傳感器,能夠收集和分析數據以改進和自主決策,從而提高效率和產品質量,減少對人機交互的需求。Caldera 說:“我們不依賴于人,幾乎所有東西都由計算機控制,我們只需將數據輸入機械并在操作開始時進行設置。” Caldera 在談到 Badalgama 的工廠時表示:“這家特殊的輪胎工廠成立不到五年,所以我們能夠獲得最新的技術,我們正在嘗試將每種材料的所有數據數字化。”盡管自動化機械的初始投資成本很高,但許多系統使用機械學習算法可以為制造商節省資金。這些解決方案可以在生產過程早期檢測到生產錯誤,從而在下游發生更昂貴的錯誤之前進行更改或修復。
韓泰輪胎機械和數字工程部副總裁 Jae Hee Kim 表示:“韓泰狀態監測系統 Plus (CMS+) 是一種設施異常預測系統,是在監測過程中實施的自動化系統。CMS+ 采用三步人工智能算法,通過收集和分析數據,提前預測設施的異常情況;它配備了基于無線通信技術的實時警報系統,以便系統在出現異常情況時,立即向管理人員發出警報。”通過在生產線中引入智能流程,不僅提高了在各自設施中工作的員工的安全性,也提高了在實際應用中使用產品的消費者的安全性。Kim 表示:“我們將人工智能應用于輪胎測試過程的自動化,自動檢測系統對輪胎內部進行詳細檢查,準確檢測輪胎內部是否存在氣泡——這是一種關鍵性缺陷。” Kim稱,韓泰計劃將這項技術擴展到整個產品檢測過程。此外,絕大多數輪胎制造商和供應商對環保運營十分關注。Caldera 解釋了如何使用高精度、自動化的 GRI 機械實現更高水平的可持續性,他表示:“主要是精確性,精確性意味著機械只自動消耗精確的配方和材料成本,因此不會因過度消耗而造成浪費。該系統的主要優點之一是可以控制輪胎規格并始終如一地制造出高質量輪胎,使其成為一個可持續的過程;還可以減少或避免過度或不足的消耗,使輪胎符合正確的規格的同時,不會浪費材料。”
Korte 表示,人工智能是未來的發展方向。VMI 目前正在開展與智能機械自動材料更換相關的新項目:“我們正在設法使機械中的材料供應自動化,并減少輪胎制造過程中的浪費和廢料。”隨著工業4.0的普及,生產現場的生產能力將逐年提高,而實際勞動力的數量將逐步減少。韓泰輪胎 Kim 表示:“通過在輪胎生產中引入更先進的自動化流程,我們見證了生產力的提高以及時間損失的大幅減少,而且能夠確保產品質量的提高以及輸出質量的一致性。此外,通過在許多制造步驟中消除或減少人機互動,可以重新分配員工的額外時間。從密煉到成品運輸過程中,工人的勞動強度逐漸降低,環境或工作質量穩步提高,從而可以進行更多的創造性工作。機械自動化和生產數字化正朝著消費者能感受到的方向不斷發展和應用。通過工廠自動化,我們能夠提供更好、更安全的工作條件。”
(原標題:VMI老總談行業發展趨勢)