日前,蘇州市首次發布綜合評價直接認定A類企業名單,正新橡膠(中國)有限公司喜獲殊榮。
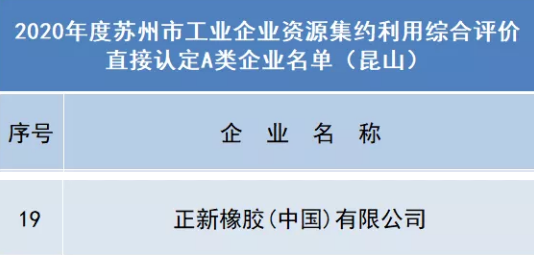
此次認定入圍名額有限且門檻較高。企業需滿足“‘世界500強’‘中國民營企業500強’‘中國制造業民營企業500強’,擁有國家級研發機構,當年凈納稅1億元以上”中的一項方可入圍。
作為行業領先的輪胎品牌,正新瑪吉斯多年來在企業智能制造及綠色化、集約化發展方面不斷深耕。此次獲評也顯示了正新瑪吉斯在這一領域的雄厚實力。
5G智能工廠實現效能升級
打造領先的輪胎智能化工廠是正新瑪吉斯制造體系一以貫之的標準,目前,瑪吉斯輪胎位于昆山的工廠已經通過5G和人工智能技術實現了數字化、智能化的轉型。昆山工廠已經全部采用智能化裝備生產, 單機生產自動化、檢測自動化、串聯自動化、倉儲物流自動化,可以做到“關燈生產”,成為了目前國內輪胎行業智能化生產的標桿。
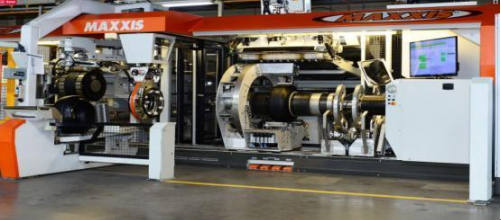
同時,在智能化工廠,從密煉到部件、成型、硫化四大工藝實現了通過AI算法計算出復雜的匹配數據,達到生產效率的最優化。使得生產效率提升40%,人員精簡25%,運營成本縮減30%,產品研發周期縮減30%,得到了行業的整體好評!
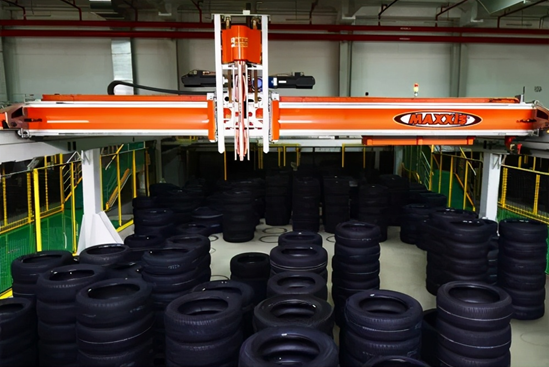
綠色化、集約化是企業持續追求
在很多人以往的印象中,輪胎行業屬于勞動密集型產業。但走進瑪吉斯的昆山工廠,卻讓很多人意外。整個昆山工廠人非常少,也沒有任何硫化品的氣味,廠區內所有機器都在有序運轉,環境干凈整潔,沒有任何灰塵,完全扭轉了人們的傳統印象。傳統輪胎行業耗能嚴重,不符合現代綠色生產的要求,瑪吉斯工廠率先引入了綠色生產理念,廠區內實現機器全自動化生產,正因為不需要人力的參與,所以廠區內全部使用自然光源,在節約能耗方面也走在了時代前沿。
輪胎制造過程中,硫化環節是很重要的加工過程,此環節會產生高溫和異味,傳統廠區內的生產人員非常辛苦勞累,還有危險隱患。因此招工一直是個問題。瑪吉斯則實現了所有步驟幾乎都由機器代勞,連入庫環節都設置了傳送履帶,自動將輪胎送往成品倉庫。成功降低60%人力需求,不但解決了人員緊缺問題,也使得招工更加彈性化,向高科技人才靠攏;全自動化標準化的生產提高了產品質量的統一度,間接提高了客戶的滿意度。

瑪吉斯歷年來打磨自身硬實力,砥礪前行。2002年就領先行業,率先引進了RFID+條碼自動化管理系統;2012年耗時5年,斥資1.5億美元打造了全亞洲最大的輪胎測試場,2018年又率先導入了工業4.0應用。2019年研發中心二期工程也已經啟用,將會持續研發市場需求的高性能產品。
工業4.0以后的瑪吉斯輪胎,產品綠色化,工藝智能化,同時降低能耗;這都是踐行橡膠行業“十四五”規劃的重要內容。瑪吉斯輪胎已經做好了準備迎接新時代的挑戰。綠色生產,智能智造瑪吉斯一直在路上。