陳新中 陳文星
丁基橡膠因其具有優異的氣密性、優良的耐熱、 耐老化、耐臭氧、耐溶劑、電絕緣、減震及吸水性而廣 泛應用于內胎、水胎、硫化膠囊、電線電纜以及防水 材料。丁基橡膠添加補強填充劑可以提高撕裂強度、定伸應力和耐磨性。
炭黑是橡膠行業選用的主要補強填充劑,丁基 橡膠所選用的補強填充劑多為快壓出爐黑(N660為 主)。筆者主要介紹N660炭黑在丁基橡膠中生產內 胎方面的適用性。
一、使用狀況
丁基橡膠、炭黑、促進劑、防老劑等在密煉機內 混合,通過密煉機的轉子及混煉室壁的剪切作用,將 以上組份轉變為一個均勻的分散體系。炭黑在膠料 中分散性好壞,直接影響了膠料的使用性能及加工性能,而影響炭黑在膠料中的分散性因素與炭黑的品質關系密切,主要與炭黑的粒徑、結構、顆粒硬度、 雜質含量、細粉含量、造粒炭黑的尺寸分布等有關。 各炭黑廠在生產N660炭黑時,其控制的炭黑粒徑、結構相差不大,但顆粒硬度、雜質含量、細粉含量及 粒子的尺寸分布有較大差異。由于內胎生產廠的配 方設計及生產工藝也存在差異,因此各炭黑生產廠所生產的N660炭黑在各內胎生產廠的適用性也存在差異。如何提高N660炭黑在丁基橡膠中的分散 性,是從事炭黑生產的技術人員需要研究的課題。筆 者利用從事售后服務及同輪胎廠進行技術交流的機 會,曾對多家丁基內胎生產廠的生產工藝進行過了解,掌握了不同內胎生產廠對N660炭黑存在不同 的使用要求,以及各炭黑廠生產的N660炭黑在不 同的內胎生產廠的使用狀況,從中得知有關N660 炭黑在丁基橡膠生產內胎的適用性經驗。下面以內胎生產廠控制的主要生產工藝參數及側重品質要求 做一簡述,由于涉及相關企業的技術機密,故對廠家 名稱給以化名用甲、乙、丙、丁、戊等表示。甲、乙、丙、 丁、戊廠內胎生產工藝過程中的混煉、加硫、過濾等工序中相關控制項目見表1。混煉的目的是為了使 得組份能分散均勻,加硫的目的是為了促進硫化,過 濾的目的是為了濾去膠料中的雜物。
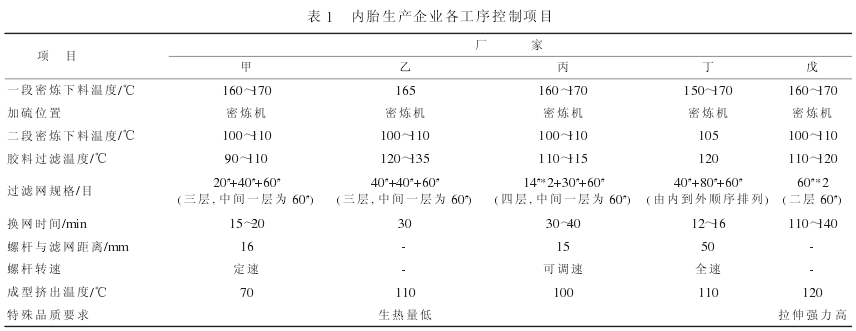
從表1可以看出,各內胎生產廠生產工藝流程 大體相當,其中的混煉過程與加硫過程的控制也相 差較小,但過濾過程差異較大,使用的濾網規格不 同,濾膠溫度有差異,更換濾網的時間相差較大。而濾膠溫度的差異直接影響生產,濾膠溫度過高,會導 致發生早期硫化,形成硬膠,易發生焦燒,表1中所列出的“乙生產廠”就存在此問題。濾膠溫度低,膠 料的流動性差,濾膠機電機功率高,濾網易損;炭黑中所含雜質量高,會堵塞濾網;炭黑顆粒硬度高,細 粉含量高,粒徑分布不均勻會影響炭黑的分散性,影 響濾膠過程,使濾膠過程延長,影響生產商的工作效 率。
二、改善試驗
本人針對N660炭黑使用于丁基橡膠的適用性 問題做了大量的試驗研究,因生產軟質炭黑的經驗 不足,對客戶要求不了解,曾付出了很大的代價。如 因N660炭黑存在100ppm的100#水洗篩余物,在甲廠使用時導致甲廠丁基內胎出現氣孔;因控制的 炭黑顆粒硬度偏高,在丙廠使用時導致N660炭黑 在丁基橡膠膠料分散不良;因炭黑生熱性較高在乙 廠使用發生膠料焦燒;因制粒品質不良,顆粒分布不均勻,影響分散性,在丁廠使用時更換濾網頻繁等。 出現的這些問題不僅給內胎生產廠帶來了麻煩,也 給本公司帶來了較大損失。經過不斷的總結經驗, 加強與客戶間的技術交流,本公司通過對生產工藝的改造,終于生產出符合各丁基內胎客戶工藝要求 的N660炭黑。下面是本公司在探索過程中總結的 經驗,供各位同行參考。
從事過炭黑生產的人都知道,因N660炭黑比 表面積較低,生產時原料油油風比較高,在生產風量 一定時,原料油處理越高,生產時結焦的可能性越 大,產品中存在焦粒的可能性越高。本公司生產N660炭黑曾有一段時間,油風比相當高,原料油在 喉管處結焦嚴重,用壓縮空氣進行霧化不足以解決 結焦問題。為了解決結焦,本人嘗試了許多方法,有 的方法雖可解決結焦,但同時出現了其它品質問題,如物理性能達不到要求,產量較低,CTAB比I2高, 著色強度高,甲苯透光率低等。最后,選擇了用蒸汽 對原料油進行霧化,采用蒸汽霧化原料油后,結焦問 題得以解決,其它品質變化很小。再將改善后的N660送甲廠使用,反饋較好。在生產N660炭黑使 用不同載體對原料油進行霧化的生產工藝條件及品 質比較見表2。
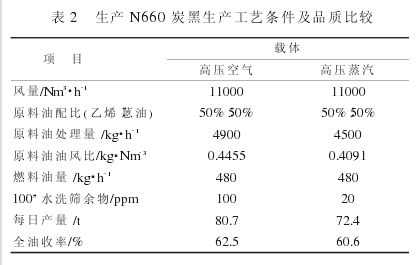
為解決造粒炭黑顆粒硬度問題,本公司不僅從 生產工藝上進行了改善,而且從檢測手段上加以控 制。在生產工藝上,本公司造粒用粘合劑原采用的 是磺化木質素,用此粘合劑,配制時溶解不均勻,易產生沉淀,經常會使炭黑顆粒硬度不均勻。鑒于此, 本公司將粘合劑由磺化木質素改為糖蜜,糖蜜為液 體,易溶解,不易產生沉淀,溶液濃度均勻。為使炭 黑顆粒硬度控制均勻,使造粒水量與粘合劑流量實行串級調節,即粘合劑流量與造粒水流量給定比例 系數,當造粒水流量發生變化時,粘合劑流量同比例 變化。在檢測手段上,從美國Tank公司進口全自動 顆粒硬度測試儀,用于對出貨炭黑硬度的檢測。改善后的產品送丙廠使用,效果明顯。
針對乙廠的生產工藝條件,本公司對供乙廠的 N660炭黑某些品質指標進行了調整。乙廠因設備原 因,在過濾時采用了較高的濾膠溫度,因此要求炭黑 的生熱量較低,因為如果炭黑生熱量高,膠料在過濾時會生熱,使濾膠溫度升高,產生焦燒。根據相關理 論與實踐經驗,炭黑的生熱量主要與炭黑的CTAB 表面積、著色強度及甲苯透光率有關,CTAB表面積 越高,生熱量越高,著色強度越高,生熱量越高。而CTAB表面積與甲苯透光率有關,甲苯透光率反映 的是炭黑表面殘油量高低。表面殘油量低,甲苯透 光率高,CTAB表面積相對較低;炭黑的著色強度取 決于原生凝聚體尺寸大小及分布。為了適應乙廠的工藝要求,本公司從改變炭黑原生凝聚體分布上降 低著色強度,使炭黑的生熱量降低。不同CTAB比表 面積、甲苯透光率、著色強度的N660炭黑在乙廠使 用情況對比見表3。

由表3可以看出,如果采用較高的濾膠溫度,應 采用比表面積相對較低、表面殘油量較少、著色強度 較低的N660炭黑較為有利。
為解決本公司N660炭黑在丁廠生產過程中出 現的堵塞過濾網、更換過濾網頻繁的問題,技術人員 經過對濾網上殘留物的研究,終于找出其堵塞濾網 的原因是由于炭黑粒子大小不均勻所致。密煉機混煉時,炭黑與膠料混合,如果炭黑粒子大小不均勻, 需要的破碎力及剪切力不同,易導致炭黑在膠料中 分散不均勻,有些炭黑成團存在于膠料中,過濾時就 會堵塞過濾網,影響生產效率。原因找出后,技術人員對炭黑的造粒過程進行了分析,認為炭黑粒子不 均勻主要是因為下料氣密閥下料不均勻,造粒機功 率波動大。因此技術人員對下料氣密閥進行了改進, 原下料氣密閥為隔板式氣密閥,間歇式下料,下料不均勻。改造后的氣密閥為平板氣密閥,連續均勻下 料。造粒時在造粒水中增加煤油,降低造粒機的功 率,增加炭黑粒子的光滑度和均勻度。對造粒粒子改 善前后的相關工藝參數及品質對比見表4。
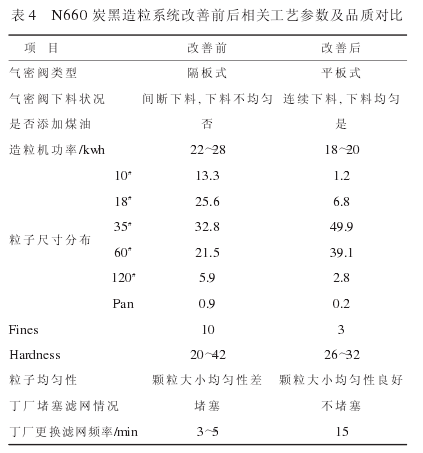
由表4可以看出,改善前,本公司N660炭黑顆 粒尺寸分布中35#與60#含量僅占54.3%,粒子均勻性不好,細粉含量較高;改善后,本公司N660炭黑 顆粒尺寸分布中35#與60#含量總和達到了89%,表明N660炭黑粒子均勻性良好,細粉含量較低。從 丁廠使用情況看,達到了其更換濾網的時間要求,表 明筆者的原因分析正確,制定的改善措施有效。
三、結論
通過一年多的努力,本公司終于摸索出了適合 不同內胎生產工藝要求的N660炭黑生產方法, N660炭黑產品深受用戶歡迎。